By Aaron Mullins - Systems Coordinator, Next Big CropGood architects are worth their weight in gold, but that doesn’t mean they know everything—particularly when it comes to growing cannabis. And now we’re looking at business operations in cannabis and beyond that could be forever changed by the COVID-19 pandemic. There’s a new appreciation of the need for physical space among workers, containment and facility cleaning. This means there are additional factors to consider such as the layout of post-harvest processing rooms and workflow throughout the facility. Here are five reasons why your architect should be working with experienced cannabis operations professionals in designing your cultivation facility for optimal efficiency and safety:
1) The Legal Cannabis Industry Is Young: Cannabis is an ancient, centuries-old trade, but it’s still a young industry with the legal market taking shape around the world. Even architects who are familiar with industrial and commercial-grade structures for growing vegetables and nursery plants generally won’t know the particulars of cannabis cultivation facility design. For example, all rooms should be built with certain space requirements in mind, which will depend on your grow method. One crucial point is that the entire layout should be based on your flower rooms. Flower rooms should all be the same size, and that will dictate the footprint and workflow of everything else. An architect who didn’t know these principles might design an otherwise excellent facility that ends up making your operational logistics very difficult to manage.
2) Growers and Architects Speak Different Languages: Growers and architects are experts in their own fields, but may have trouble getting on the same page when the grower is trying to communicate their needs. When it comes to designing your cultivation facility, it helps to have a translator. A design consultant can help iron out any miscommunications and clearly articulate the grower’s needs across the facility, which streamlines the process and often prevents a lot of wasted effort and frustration on both sides. Furthermore, growers may lowball the cost by giving estimates based on the facility’s minimum workflow. You need to design for maximum throughput so your environmental control systems can keep up through the end of the flower cycle. Otherwise, problems will arise due to increased potential for mold, mildew and other issues.
3) You Have to Keep Your Cool: Your architect will know that your facility has cooling and dehumidification requirements, but someone in the design process needs to know exactly how much is expected, so that your HVAC and utilities can be properly planned for. Furthermore, calculating design needs based on the square footage of the facility or even how many plants it will hold is not enough. There are numerous variables to consider, such as how facility heating and cooling changes when the lights are on versus when they are off, and what kinds of lights you are using (high-pressure sodium (HPS) versus LEDs, which require less cooling but change the humidity levels of the room).You also can’t expect your architect to be able to determine your cooling and dehumidifying needs based on how much power and water you’re going to use. For example, if the grower tells the architect they’re going to use 1,000 gallons of water a day and 40,000 watts for lighting, the architect won’t understand what that equates to for utilities and spatial needs.
4) Cannabis Facilities Have Unique Safety Concerns: The Occupational Safety and Health Administration (OSHA) has been paying more and more attention to cannabis facilities, and that’s a good thing—this agency is there to ensure the health and safety of your workers. Because this industry is new and the regulations newer, most architects won’t know the specifics of safety and OSHA regulations.Airflow is one key example: The facility must be designed with good airflow throughout or workers could have breathing issues in certain areas, particularly where evaporative solvents such as isopropyl alcohol are present, or when there is fine plant particulate matter floating around. Improper airflow puts your employees at risk and is going to be a major pain to deal with after the fact if equipment retrofitting needs to happen.There are also specific requirements around ergonomics. In some cases, rooms need to include benches that are no more than 4 feet wide, with aisle spaces of at least 30 inches (it’s possible these standards may change in the wake of the coronavirus pandemic).The current requirements are doable, and will make your workers’ lives better in subtle ways, including not feeling like they’re being crammed into a space, day in and day out.
5) Design Your Cultivation Facility With Laboratory-Grade Standards: Your cultivation facility needs to be designed for maximum workflow and minimum pathogen spread. That means you need to keep certain areas separate. Your post-harvest processing and packaging area ought to be sequestered, along with flowering, vegetation and propagation areas. This allows you to control any potential outbreaks of pests, fungus or mold, which is especially important because you can’t simply use pesticides to spray away the issue. To produce medical-grade flower, you need to have a laboratory-grade facility, and most architects and engineers won’t know the specific requirements involved with this. By bringing in a consultant, you can have an optimally designed facility from Day One. The more your facility factors in the needs of your operation and your employees, the easier time you’ll have hiring and retaining workers, and producing large quantities of fantastic flower.
Learn more about Next Big Crop’s comprehensive consulting services.
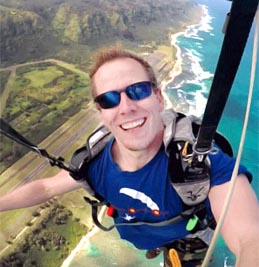