By Aaron Mullins, Systems Coordinator at Next Big Crop
The topic of “humans vs. machines” definitely has some sci-fi undertones. But in automating cannabis cultivation, “humans helped by machines” is a lot more accurate—and mutually beneficial for facility owners and their employees. Automation serves a dual purpose: On one hand, staff can focus on what they do best in achieving optimal plant care, efficient growth and harvest workflow. On the other, owners can reduce labor costs for cannabis cultivation while ensuring operations run smoothly—even in challenging circumstances such as reductions in workforce or staff turnover. To integrate automation into the workflow, there are a few places where facility owners should look closely, including irrigation, facility environmental controls and harvest processing.
Reducing Labor Costs for Cannabis Cultivation
Owners often don’t have the funding they want (or need) to get their ideal facilities online, so they try to save money wherever they can. While fully human-powered operations get the job done initially, this approach becomes unsustainable because it limits the ability to scale and introduces a glaring vulnerability—owners rely too heavily on just a few people with critical knowledge of the grow process. If owners can automate certain processes, they are more empowered across the operation and it becomes easier to handle challenges such as key staff leaving, or dire circumstances that could prevent several workers from coming in—think family illness, floods, wildfires, etc. (Speaking of workplace challenges, the coronavirus pandemic has sparked unique operational changes for cultivators, which we addressed in detail in this blog. Automation can quickly pay for itself in labor savings and productivity, and it provides better flexibility in training staff to accomplish detailed tasks. And more consistency in the day-to-day operations means more consistent yields.
Simplify Complex, Time-Consuming Tasks
Irrigation is a prime example of a detailed task where automation is a huge time saver.
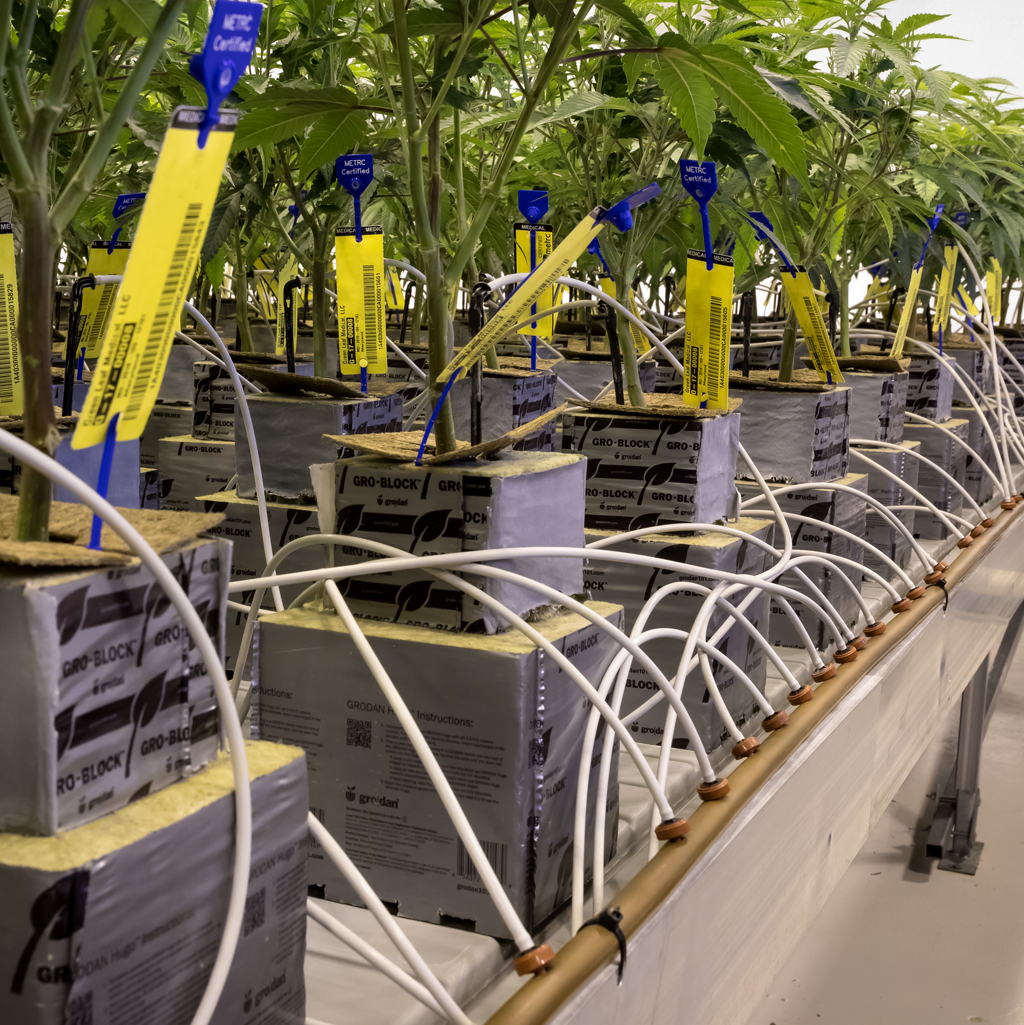
Instead of hand mixing batches of nutrients and hand watering, you can have a computer blend your nutrients. This means all employees have to do is keep the nutrient tanks full. Think about it: Instead of paying someone to mix batch tanks daily by hand—this task alone can consume many hours of an employee’s workday—a computer gets the job done in less than an hour. Further, automated irrigation provides consistent application based on the needs of the plants at various growth stages. Letting technology do the heavy lifting with environmental controls also provides a good measure of peace of mind for owners and cultivation managers. With computer-run monitoring for lighting, humidity and room temperature, the cultivation manager and other key staff can be looped in at all times without having to physically be at the facility. If there’s any kind of issue, such as an overnight power outage or HVAC system hiccup, receiving an alert remotely gives you the ability to address it faster—and provides more of a buffer in catching potential mechanical problems before they lead to an overheated flower room where the plants get cooked and there are hundreds of thousands of dollars hanging in the balance.
Where the Human Touch is Essential
With automation assisting employees, their valuable time can be utilized more strategically: They have more bandwidth for monitoring plant health and tending to plants with necessary pruning, for example. They’re scouting for issues related to Integrated Pest Management (IPM), such as harmful pests, mold and mildew, and mitigating problems before they get out of hand.
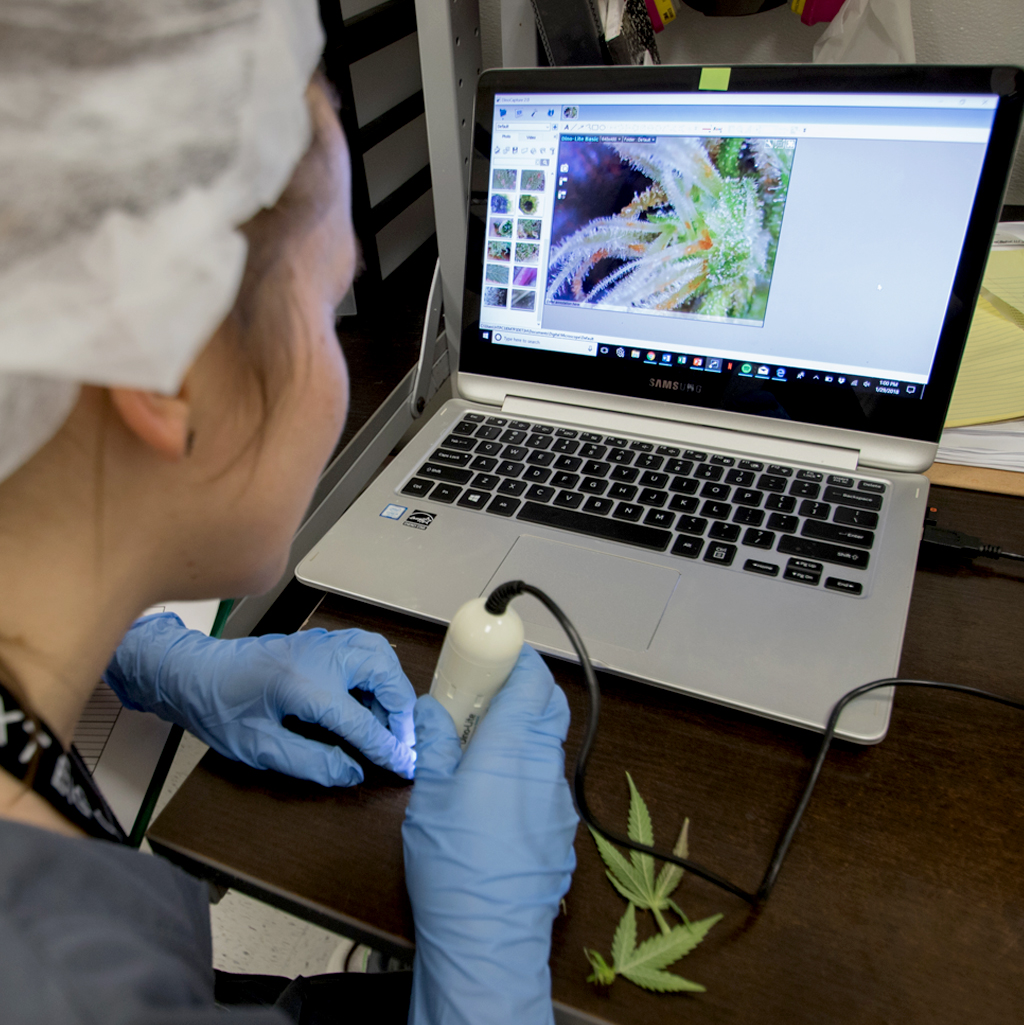
And they’re dedicating their time and attention to the most valuable component of cultivation—the harvest process. This final phase requires significant human labor because sensitive flowers need a delicate hand, and the veg and flower rooms need to be properly cleaned, disinfected and prepared for the next cycle. That’s not to say harvest is excluded from the benefits of automation. For example, after plants are cut, machines can take over with weighing, and instead of requiring 10 people to accomplish this, two people can ably do it. As a facility owner, you also benefit in being able to invest in top-quality employees and reduce turnover. Having a scrappy crew of 10 highly skilled and appropriately compensated employees is much better for business than 20 minimum-wage workers who aren’t committed.
Scaling Up and Bottom-Line Considerations
In Next Big Crop’s development of more than 2 million square feet of cannabis production space across the U.S., one truth is evident: For facilities with 5,000 to 10,000 square feet of canopy, automation is more of a necessity than a “nice to have.” And automating processes is a key stepping stone to scale while keeping labor costs for cannabis cultivation in check. Integrating automation into your daily operations is a smart play for today—and the future. For modern cannabis cultivation facilities to succeed and expand, especially in the increasingly competitive wholesale markets we’re seeing develop coast to coast, automation should not be a fantasy. It needs to be the reality.
Learn more about Next Big Crop’s facility design and automation consulting services.
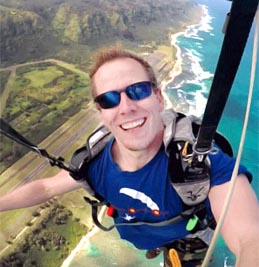