By Aaron Mullins, Systems Coordinator, Next Big Crop
I’ve experienced my fair share of growing pains in cannabis. In this industry, who hasn’t? Expanding an indoor grow operation, building out a new facility, taking on a full-scale renovation: These things require planning and deep cannabis cultivation knowledge—and if executed improperly, they can lead to big delays, cost overruns, missed harvests or worse.As a systems coordinator at Next Big Crop, it’s my job to be on the front lines with our clients as they navigate facility expansions, retrofits and growth in our exciting and rapidly expanding industry. A key differentiator? We tap into our expertise forged firsthand to help clients successfully grow their businesses—not just out-of-context spreadsheet numbers or best guesses. Our years of experience building and supporting cannabis businesses have helped us learn in very real terms what works and what absolutely does not, and it’s our mission to spread the word.Our recent acquisition of SevenFive Farm, a boutique Colorado cultivator, underscored the importance of attention to detail and understanding your limiting factors up front. I’ll walk you through what we’ve learned upgrading this network of four greenhouses, with a focus on increasing production and introducing new efficiencies.
Lesson #1: Water Availability, Sufficient Pumps and Drainage are Key
Good-quality water—and how it gets to your plants—will make or break your cultivation operation. When you’re upgrading or retrofitting a cannabis grow, take a good look at where your water is coming from (ideally, a municipal source), how big the pipes are, how big your system’s pumps are and the drainage system. Once you have a better idea of your facility’s plumbing and drainage capabilities, you can plan out upgrades and fixes by order of importance.When we were upgrading the infrastructure at SevenFive Farm, we realized we’d need to address water availability and power to ensure enough water was actually making it into the irrigation system and getting to plants in each of the four greenhouses. And drainage? The facilities were equipped with gravel floors and needed upgrades and new piping to ensure water was being carried away—not pooling below the floor’s surface. More on that later.We tackled the irrigation system first. This simple upgrade made the facility so much more efficient, and set the groundwork to solve some other issues in the space. For example, ideally we’d have 1.5-inch pipes carrying our water—right now, we’re working with quarter-inch pipes, which makes our water system behave more like a bunch of individual creeks rather than one central river.And we’ve had to come up with some creative solutions for our pumps, which aren’t quite up to our standards as far as power output goes. Replacing the pumps is an expensive endeavor, and it’s also not an urgent need for the facility. But because we evaluated the system’s entire footprint, we’re able to forecast spending and set our upgrade schedule, saving us a headache down the line.
Lesson #2: Electrical Can Be Tricky—Here’s How We’re Handling It
In our daily lives we take electricity for granted and expect on-demand power for our appliances, electronics, air conditioners, clothes dryers and hot tubs—often simultaneously. And we’ve all been in a situation where a circuit gets overloaded, and all of a sudden, it’s lights out.While you can fix this situation pretty easily at home, if your cultivation facility is maxing out your electrical system regularly, it’ll take a lot more than flipping a breaker switch to get it back online.Put plainly, it’s never a good idea to ask an electrical system to perform at absolute max capacity for hours and hours at a time for months on end.And when you’re upgrading or retrofitting a facility, the significant downtime required to fix or replace an electrical system could translate to tens of thousands of dollars of lost revenue and productivity.Owing to productivity increases over the past few years and subsequent increases in demands on the electric system, the SevenFive Farm facility requires an electric upgrade, and we’ve put together a solution that will fix the system and minimize cultivation interruptions.I’m currently building a bigger, newer electrical system for the facility. The plan is to wire in the newer, more robust electrical infrastructure for the entire farm. Once the new system is in place, I can use it to provide power as we switch over each greenhouse, minimizing power interruptions to keep production on track until the new system is fully online. It’s a somewhat complicated workaround, but it’ll make optimizing efficiency in each greenhouse so much easier—and prevent any loss of revenue or productivity during this upgrade.
Lesson #3: Evaluate the Basics: Floors, Ventilation, Filtration Capacity
If you’re retrofitting an existing grow operation, it’s all too easy to assume that foundational basics like floors and ventilation will be fully functional and up to your standards. But it’s common for facilities, especially as they increase production, to need bigger, better solutions.Your ventilation and air-filtration systems are critical—for plant and worker health.In our facility-wide assessments, we discovered that many of the processing areas had low ventilation, which meant dust, mold, bugs and pathogens could become concentrated in areas where workers performed their tasks. We made sure masks were always available to workers in these areas and began filtering the air using Merv 11 filters, which capture spore particulates, remove 95% of pollutants from the air and are substantially cheaper than HEPA filtration systems. If your facility has an existing HEPA filtration system, I highly recommend using prefilters, otherwise you’ll run the risk of wearing out the entire system quickly without them.I told you I’d revisit the gravel floor situation—here we are. When we first purchased the farm, we realized the greenhouse floors were fully gravel. That meant that when it rained or snowed, the moisture found a way to bleed into the facility through those gravel floors, making humidity control a problem.Right now, we’re working to get some gravel floors (in a facility that’s right next to a large pond, no less) replaced with concrete to provide a better barrier against moisture and prevent any issues in the future. Because of the pressure exerted by the water-saturated ground, any water we allowed to fall on the gravel floor didn’t have anywhere to go. Our current solution, until we can pour concrete, is to build solid tables with gutters that can carry water away from the room.As with nearly any major project, these kinds of upgrades often require permits, which can be a time-consuming, frustrating process. We recognized this need right off the bat, so we’ve had a jump-start on getting needed approvals. But if you don’t know to look for these kinds of fixes, it could translate to a major pain as you wait for permits to wind their way through local bureaucracy.
Lesson #4: Local Buy-In is Key
Put simply, if the jurisdiction you’re in has only reluctantly embraced the cannabis industry, you’ll find it difficult to move forward on any upgrades. As I mentioned, we’re working with local agencies on a permit to allow us to pour a concrete floor, but a few minor setbacks and delays have been inevitable.I speak from experience in saying that it's better to be diplomatic than antagonistic. As you explore a retrofit or expansion of an existing cannabis operation, I encourage you to make inroads and forge relationships with county and local officials. Show up to public forums, begin conversations with officials early on and demonstrate your commitment to working with them. And it never hurts to ask for an introduction or for advice from other local cannabis professionals.Beyond that, it’s essential to understand regulations in your local jurisdiction or county, including the number of cannabis plants you’re allowed to cultivate at any given time and requirements for filtration, security, building materials and the like. When the time comes for upgrades, expansions or retrofits, you’ll be prepared—putting you way ahead of the game.
Lesson #5: Choose Your Contractors and Engineering Partners Wisely
Contractors and engineering partners who have good relationships with local cannabis regulators will save you a lot of time and energy down the line. Even having everyone in the same meeting is a huge win—once we found the right partners in our upgrade efforts, we were able to get everyone on the same page, quickly, which resulted in much faster movement on major projects.Keep in mind, if a deal sounds too good to be true, it probably is. While being mindful of your finances is important, it’s more important to ensure you’re working with good, competent vendors. Spending the time to thoroughly vet them, even if it sets back your project timeline slightly, will be worth it in the end.
Key Takeaway: Due Diligence Pays Off
When we purchased SevenFive Farm, we moved on a huge opportunity. We’ve been fortunate in that most of the necessary upgrades have been relatively straightforward.If we could do it all over again, we’d definitely take a closer look at things like the electrical system and drainage. Having a good understanding of any such “limiting factors” shouldn’t scare you—in fact, just the opposite. Knowing what you’re starting with allows you to have more bargaining power during a sale and can help you accurately forecast upgrade timelines, harvests, business expansions and so much more.I can’t emphasize enough how important it is to lean on people who have specific expertise on commercial cannabis facility retrofits and upgrades. Why not learn from those who have gone before you? You’ll save time, money, and sidestep pitfalls while you take your business to the next level.
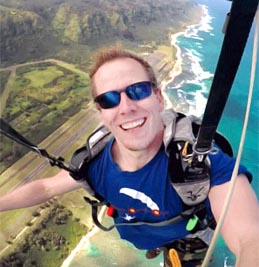