By Aaron Mullins – Systems Coordinator, Next Big Crop
Many businesses use data collection to help improve their performance and reduce operating expenses, and cannabis cultivators should be no different.
Data can help you monitor and easily control the environment in which your marijuana plants are growing, leading to more consistent yields and higher-quality output when the growing conditions are based on a strain’s particular needs. And here’s something equally critical: Cannabis cultivation data collected throughout your facility can give you a clear picture of your operation’s productivity and enables you to better mitigate loss and enhance efficiencies.
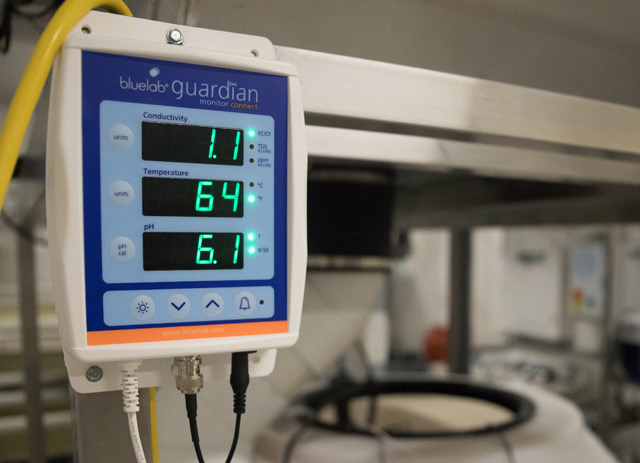
You’re used to tracking how every penny is spent in your operations, so why not track how you’re actually making your money?
The more you know about your facility’s environmental factors, from the ambient temperature in the rooms to the amount of carbon dioxide that’s available for plant growth, along with water and lighting, the better off you’ll be when it comes to scaling and investing in equipment upgrades.
Cannabis Cultivation Data: Where to Start
Many facets of a cultivation facility can be tracked, but the key metrics to record in a grow room include:
- Temperature
- Relative humidity
- Carbon dioxide (CO2) concentration
- Light
- Vapor pressure deficit (VPD)
- Water content in the growing media
Tracking such data can help you figure out what works best and really dial in optimal growth conditions for maximum production, particularly with flagship strains that are grown continually.
Many cultivation facilities take a low-tech approach, where employees are responsible for writing down the temperature and humidity levels in the grow at designated hours of the day and entering it into a spreadsheet to get basic metrics. Obviously, this task can be time consuming and prone to human error. And at the end of the day, this information is limited in its utility.
Digitally collecting cultivation data can be as simple as installing environmental sensors that monitor the temperature and humidity in your cultivation facility’s compartmentalized grow rooms, or as elaborate as a full-control system that monitors the amount of light your bulbs are emitting (or natural light coming through the greenhouse roof) and how much CO2 is getting into the room.
Cannabis Cultivation Management: System Options
If you haven’t been capturing data before, the two most important things to start with are temperature and humidity, hands down.
Basic Control Systems
You can get nice temperature and humidity monitors with detachable probes at your local GrowGeneration store. The detachable probe will enable you to measure all parts of your cultivation facility, which can also help you adjust for issues within your grow.
Like most technology, there are different grades of equipment that you can use to track the environment in your facility.
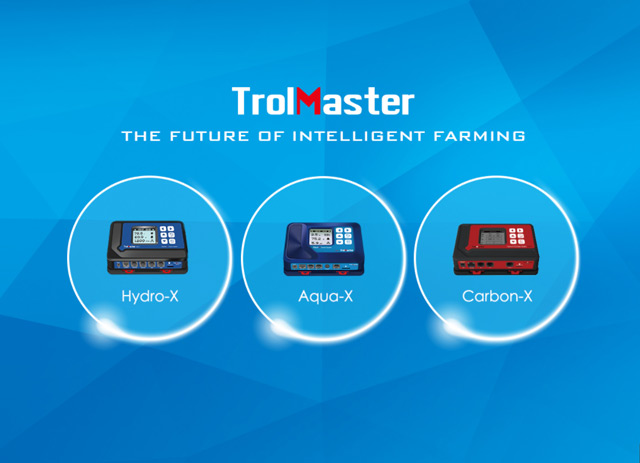
A step up from the simple probe-and-monitor system is a basic control system such as TrolMaster that lets you check temperature, humidity, CO2 and the water content of your growing medium. In addition to tracking environmental data in the room, a decent digital control system also allows you to monitor equipment usage, which is key for efficiency metrics. When I use such systems, I can keep track of things like how often air conditioners and heaters are turning on and off. And systems that monitor multiple zones inside a single room will alert me when any of the individual units within a zone are starting to fail, forcing the other units to work harder.
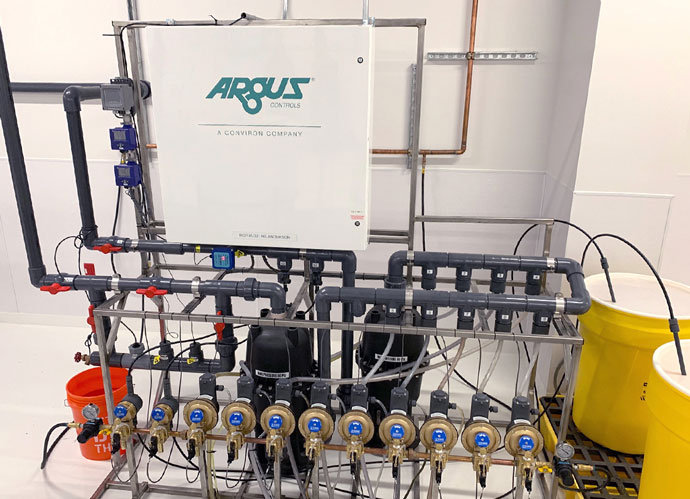
Advance Control Systems
A full-control system is the Cadillac of technology for cannabis cultivators. In addition to what a basic control system can do, full-control setups such as those manufactured by Argus, Wadsworth and Priva capture statistics relative to light, including how much light is coming into the greenhouse or how much light your bulbs are putting out, which helps to dial in a more cost-effective bulb replacement schedule, for example.
Any sensor can be incorporated into an automated full-control system. You can dump CO2 onto a wet wall in your greenhouse and check your CO2 sensor to understand how much is actually going into the room and working for the plants.
One particular dataset that’s worth keeping an eye on with a comprehensive full-control system: Measure the vapor pressure deficit (VDP), which is the difference between the amount of water vapor the atmosphere is able to retain—which depends on temperature—and the amount of water vapor contained in it (relative humidity). The correct VPD will increase the plants’ activity and improve their growth, enabling them to reach their full potential during the flowering phase, optimizing yields.
Cannabis KPI Optimization: Using Grow Data Effectively
Monitoring data from your cultivation facility lets you see what’s working so you can lock it into your processes—and weaknesses that should be remedied so you’re maximizing every cannabis production cycle with customized adjustments depending on the cultivar.
Keep track of everything with your cannabis production measurements: Document when your CO2 ran out or when you lost an AC unit—any information tied to decreased yield or incurred loss is valuable.
When you make changes to your facility’s temperature, humidity or lighting, having the historic grow data can help you analyze whether changing the variables improved your harvest or not. You’re essentially tracking the facility’s key performance indicators (KPI), to use a business-school term, which is a smart strategy when it comes to scaling the facility’s production capability.
Before investing in an automated system, do a cost analysis to make sure it’s justified. Keep in mind what your margins are and whether you can monetize the equipment. If you do decide to purchase a control system, spend the time needed to dial in the equipment so everything works properly and your data collection on your cannabis grow and yield is rock-solid for future planning.
Want to learn more about control systems for cannabis cultivation? Next Big Crop has answers, contact us anytime.
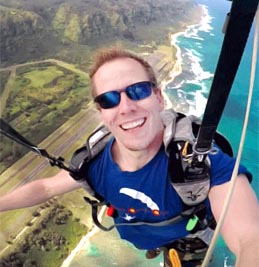