By Aaron Mullins—Systems Coordinator, Next Big Crop
Many people start their cultivation facility on a shoestring budget with the intent of scaling up their operations after they’ve made some money.
But scaling your cannabis business can be expensive, so you need to make sure that any of your investments in new equipment or facility upgrades enable you to bring in more money for less effort.
First and foremost, you need to figure out your budget. You could spend $1,200 on lighting controllers, up to $4,000 on new fans and as much as $20,000 on a new nutrient injector system. If you want a full-control system, you’ll be forking out up to $50K. Construction improvements are even more expensive—upgrading from gravel to concrete floors and installing drains could cost as much as $100,000.
Always ask yourself whether the upgrade is something that will increase profitability and productivity, or is it just a shiny new thing or change for the sake of change.
Being strategic is everything: When you couple your five-year business plan with investments in targeted areas, you’ll achieve your ROI much sooner. Here’s how to approach scaling up cannabis production the right way:
Assessments for Grow Op Scaling
The first thing to do if you’re planning to upgrade your operations is to literally clean house. Deep clean everything—change filters, wipe that thick layer of dust off the fans, clear the leaves off the floor and make sure standing water is mopped up so it’s not causing mold. Taking a really close look at your facility from top to bottom can be illuminating.
The next step is to identify and evaluate where the problems are in your production and facility operations. For example, if you notice that every time you grow bigger plants you start getting mold or rot, you likely need more air circulation, so an investment in bigger and better fans would be prudent because you can optimize yields. Or if you’ve spent a lot of money in the flower rooms, purchasing an automated trimmer that doesn’t call in sick could be a better bet than paying 20 people to do that job every harvest.
Whatever you do, you should introduce new elements slowly so that the entire facility operation isn’t at the mercy of the changes. It may even be prudent to establish a research and development area to test the systems first.
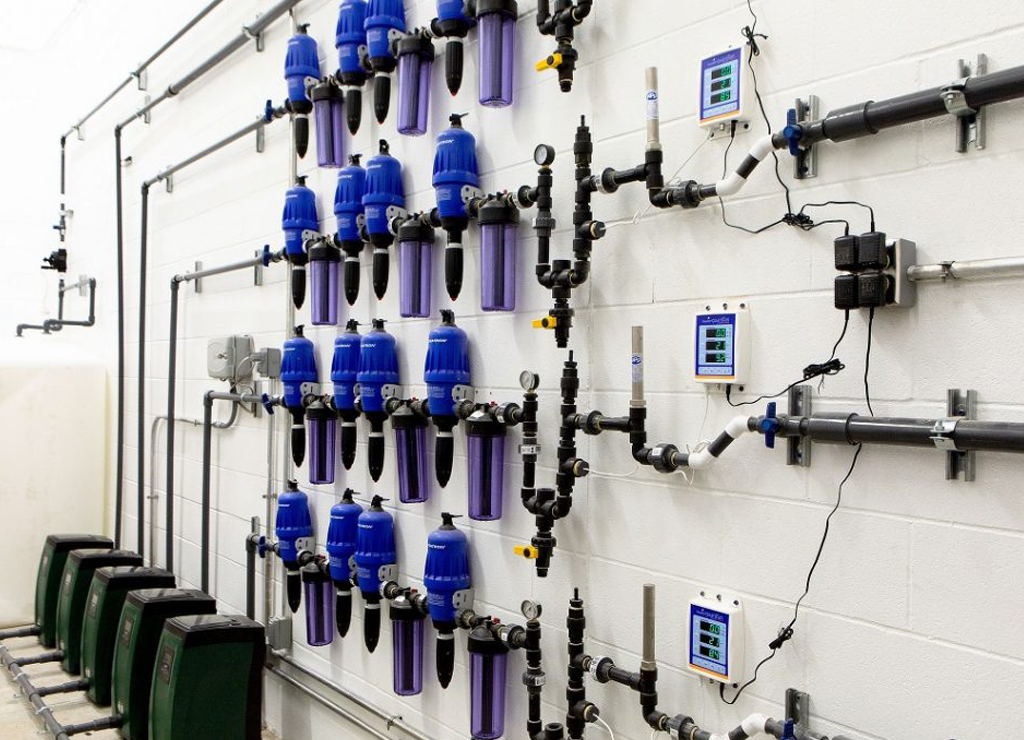
It’s unlikely that everything in your cannabis production facility needs to be upgraded, so be sure to assess what you’ve got that’s working well, while identifying areas of weakness and how you can improve them, such as through automation or a different methodology. If your staff is spending a lot of time scrubbing pots, maybe you should purchase compostable cloth versions. Or if you’re mixing nutrients by hand, investing in a Dosatron injector would likewise save labor and increase consistency in your operation.
Have a Plan for Implementing New Changes
Proceed with caution when introducing any new equipment to your grow facility, whether it’s a soilless system, fertilizer injectors or different lighting.
Upgrading to new lights may be tempting—technological advances have enabled today’s lighting systems to produce more lumens while using less electricity. Some even let growers customize light spectrums.
But there’s a lot to consider before introducing your plants to a new light source. First, if you’re moving from a lower wattage to a higher wattage, you should test the system to be sure it doesn’t stress your HVAC system and cause excess heat to burn the plants.
Many growers are attracted to advanced hydroponics systems because they use less water and reduce the risk of soil-borne diseases. But making the switch away from soil can be tricky. You have to maintain strict control over water temperature and dissolved oxygen levels. It’s not uncommon for a hydroponic system’s spray nozzles and tub junctions to clog or leak.
Stay Consistent Companywide
For some cultivators, scaling up goes far beyond increasing production at an existing facility. It means setting their sights on scaling up cultivation facility design at multiple operations in several states. So, when they are making improvements to one facility, they need to be able to replicate their success across the company.
You might see your company’s expansion into a new market as an opportunity to start anew with your commercial grow room design plans and try the latest-and-greatest racking system, LED lights, rolling benches and fertigation system all at once, but it’s best to control the variables within your company’s facilities to ensure consistent, high-quality output.
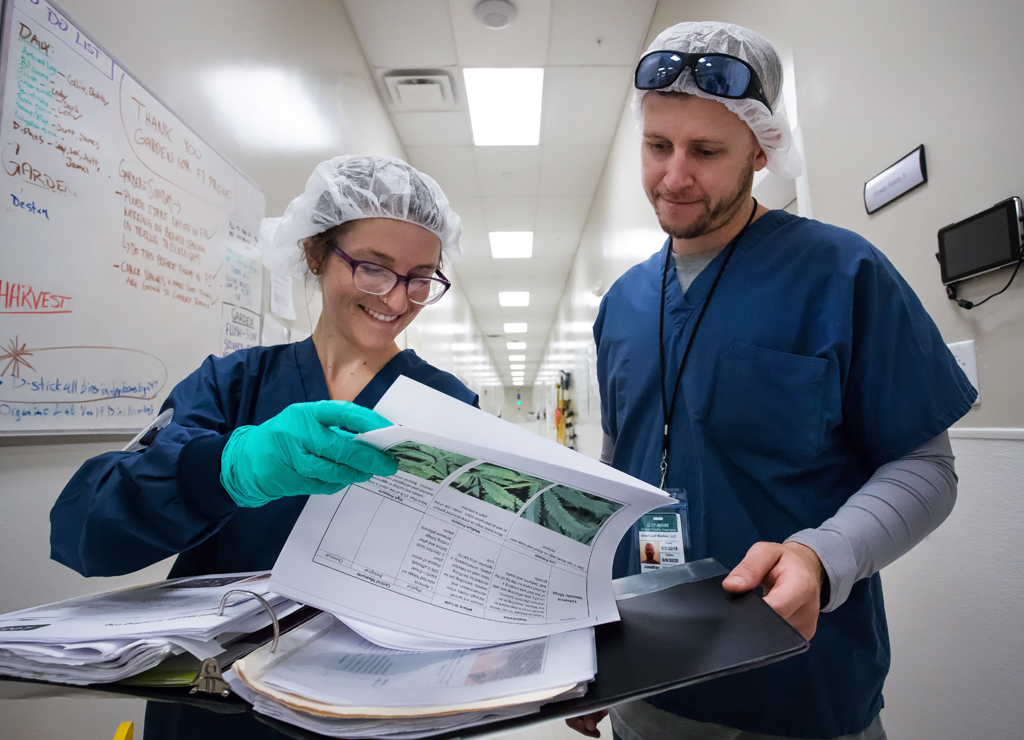
Avoid widespread variations in how facilities operate. That means having companywide standard operating procedures (SOPs), using primarily the same equipment from one facility to the next, keeping your feeding schedule protocols the same and basically tending to your plants the same way as you do in every facility.
Scaling up your cannabis operation may seem overwhelming, especially when daily operations are a nonstop churn. It can be difficult to identify key operational weaknesses when you’re in the thick of it. If that’s the case, you can hire a cultivation services specialist to assess your facility’s strengths, observe your processes and identify areas where upgrades would yield major benefits with labor savings and optimized efficiency.
We’re happy to talk shop at Next Big Crop about equipment and materials sourcing. Contact us here.
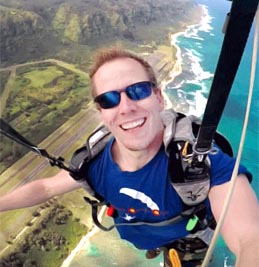